Dumaplast Interior PVC Wall Cladding
Project deliverables were to design and start up a production extrusion line in Dumaplast facilities in Maldegam, Belgium for a new product applying the MuCell(tm) process..
Redesign of the extrusion process targeted decreasing material by 10%, increasing production rate while maintaining stiffness and acceptable Class A surface. (See Journal of Cellular Plastics abstract below right for more information)
I was on-site over a period of 5 months supporting hands-on the startup of this new product and process.
Dumaplast became an investor in my company.
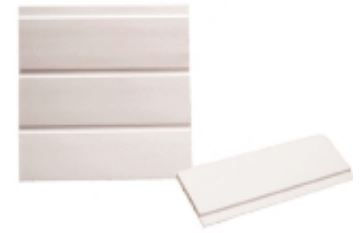
From Vanvuchelen, J. et al. Microcellular PVC Foam for Thin Wall Profiles, Journal of Cellular Plastics, Volume: 36 issue: 2, page(s): 148-157
ABSTRACT
Loss of toughness is a major obstacle for applications of foamed rigid PVC, especially for thin products. With cell sizes below 100 μ, microcellular PVC foams provide much higher toughness while creating new products with thinner walls than those possible with conventional PVC foams. In this original work, a thin-wall microcellular foam PVC product was obtained by the application of the MuCell® process on a commercial scale extrusion line [1]. The process consists of the injection of supercritical fluids as blowing agents into the extruder. The screw and die were modified to achieve single-phase solution and cell nucleation. Foamed thin wall profiles with a thickness of about 0.45 mm were made with a density reduction of up to 30%. The cell size obtained is typically much smaller than 100 μ with little interconnectivity. The profile showed excellent toughness, with a tensile elongation typically higher than 60%, and smooth surfaces